What are the Benefits of Wearable Health Devices? Wearable health devices have revolutionized the...
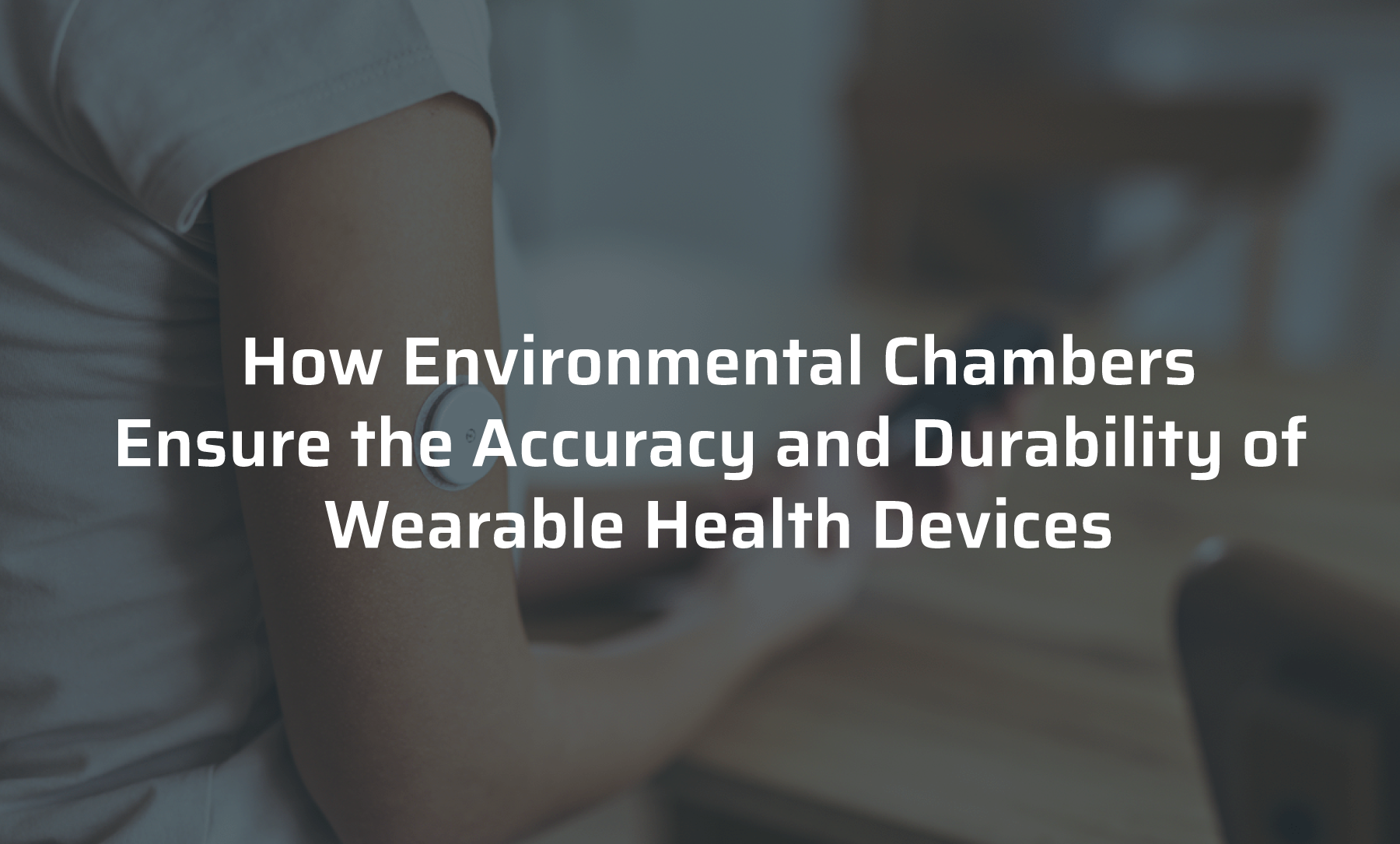
What are the Benefits of Wearable Health Devices? Wearable health devices have revolutionized the...
Batteries play a fundamental role in our world. From powering an everyday laptop to energizing an...
AI Technology for Environmental Test Chambers The rapid advancement of technology, driven by the...
2025 Battery Conference Associated Environmental Systems was back in action this month in Orlando,...
Are you on the lookout for your next environmental test chamber? Or maybe you’ve never purchased...
Does Cold Weather Affect EV Batteries? Cold weather introduces unique challenges for electric...
Solar Panel Testing Solar technology continues to make incredible breakthroughs. As the world...
Environmental Test Chambers for the Packaging Industry Packaging impacts our everyday lives....
Leading Environmental Test Chamber Manufacturers As 2024 comes to a close, we look back at a...
AABC Conference Top Industry Leaders Just a year ago, our team at Associated Environmental Systems...