How to Buy An Environmental Test Chamber
The considerations and steps to take when purchasing an environmental test chamber
Buying an Environmental or Battery Test Chamber
Strategic decision-making must be aligned with budgetary constraints and timelines in any project. Consider the choice between outsourcing environmental testing and purchasing a test chamber. Outsourcing may initially seem attractive due to access to seasoned engineers who can aid in developing test protocols and addressing failure issues. The substantial hourly testing rates, potentially reaching $1,500, could escalate costs significantly if extensive testing is needed.
For instance, Segway opted to purchase chambers, including a drive- or walk-in environmental chamber, for $150,000. This upfront investment yielded a break-even return within 18 months and facilitated a more time-efficient schedule, accommodating additional tests when required.
Benefits of Buying Environmental Chambers for Your Testing Needs
The benefits go beyond time and money, too. When you're developing new-to-market items, your in-house team will likely be the best expert group. Each project division can work together to make educated decisions and adjustments. Also, in today's fast-paced marketplace, waiting for scheduled testing time over many iterations gives competitors a chance to beat you to the market.
There's also a greater level of protection. The ability to test in-house as often as you like limits the chances of a costly product recall. The likelihood of one today is significantly higher than in previous years ago, with better detection tools and stricter safety rules in place. The U.S. Consumer Products Safety Commission (CPSC) averages one daily recall. Recalls.gov, a collaborative effort of seven U.S. government agencies, admits more recalls need to be listed. If your product were to be recalled, it's not the testing supplier that gets the bad reputation; your company will face the backlash.
While the advantages of owning a test chamber are apparent, it remains a substantial capital investment that demands careful consideration. This is where Associated Environmental Systems comes into play. Our comprehensive guide is designed to assist you in making informed purchasing decisions and explore customization options tailored to your specific needs.
DETERMINE YOUR TESTING REQUIREMENTS
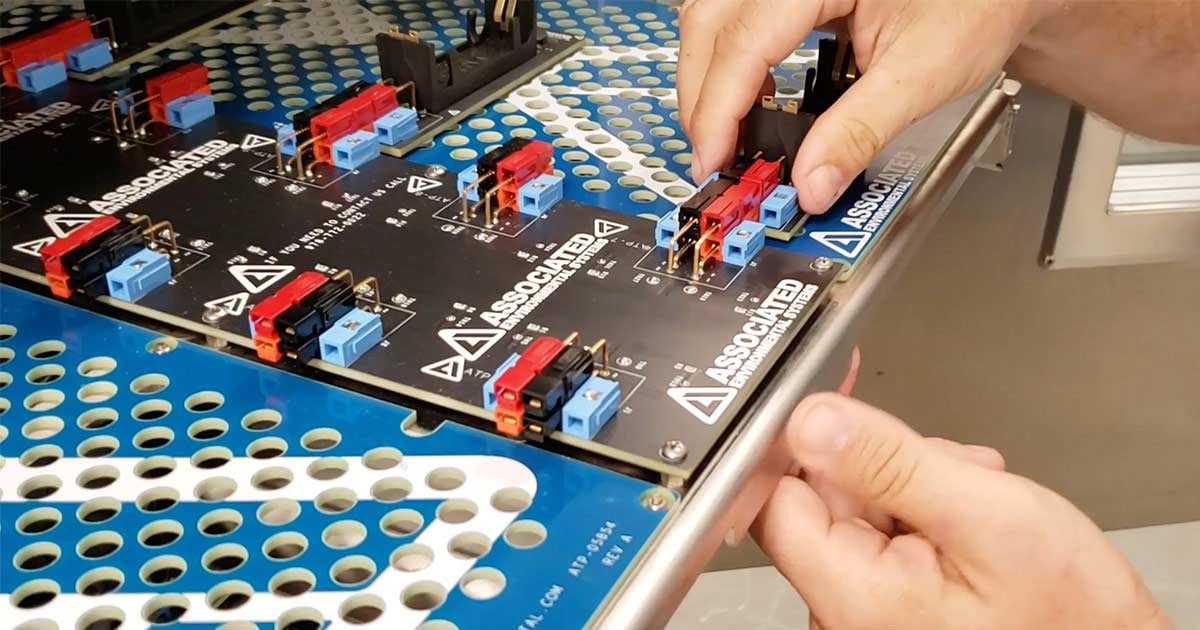
YOUR TESTING REQUIREMENTS MAY BE DICTATED BY GOVERNING BOARDS, INDUSTRY STANDARDS, OR CONSUMER EXPECTATIONS.
Your company has developed a new product. Now, you need to select an environmental test chamber to make sure the product will perform as expected in real-world conditions. The product must be tested at various temperature and humidity conditions to ensure its quality and reliability.
Where do you start? What will determine your selection criteria?
Research and Development Testing
If you’re testing in research and development (R&D for short), consider how the different elements can be tested to shorten the development time by identifying the shortcomings of components. Environmental test chambers feature precise temperature and humidity controls to create repeatable climate conditions.
The most common tests run are for product shelf life, accelerated life testing/reliability testing (HALT/HALT testing), and stability and package testing. These tests can be run using temperature for repeated thermal cycling and humidity to find weak points.
Identifying defects or stress limits during this process leaves room to redesign the product (if need be) and set performance expectations.
You know when your milk will expire through the FDA’s required date stamping. However, most consumer products don’t have expiration dates, and companies are left to self-govern themselves.
Additionally, industries have their own test specifications. These are self-regulated through organizations or adhere to government regulations under applications like light exposure, corrosion, military standard testing, temperature evaluation studies, electronic component burn-in, plant growth, and insect rearing, to name a few.
Production Testing
During production, companies either sample test products from batches or lots, or test every product that comes off the line with highly accelerated stress screening (HASS testing). This form of testing involves pushing the product to its identified stress limits determined by the HALT testing in the development phase. HASS testing is crucial because it will likely spot improper manufacturing processes. There’s a chance that the product fails during manufacturing due to unreliable components that could have been identified in HALT testing.
It’s common practice to test products that contain Lithium-Ion batteries during production. Automated external defibrillators (AEDs), flight recording devices, mobile/cell phones, and many more products are tested during production. Finding defects during manufacturing is much more costly, and it’s more challenging to identify where the failures are occurring. Therefore, it’s beneficial to put more time and resources into development testing. Customer expectations will determine the need for batch sampling or total production testing, as this varies by industry.
CHOOSING TEST CHAMBER SIZE
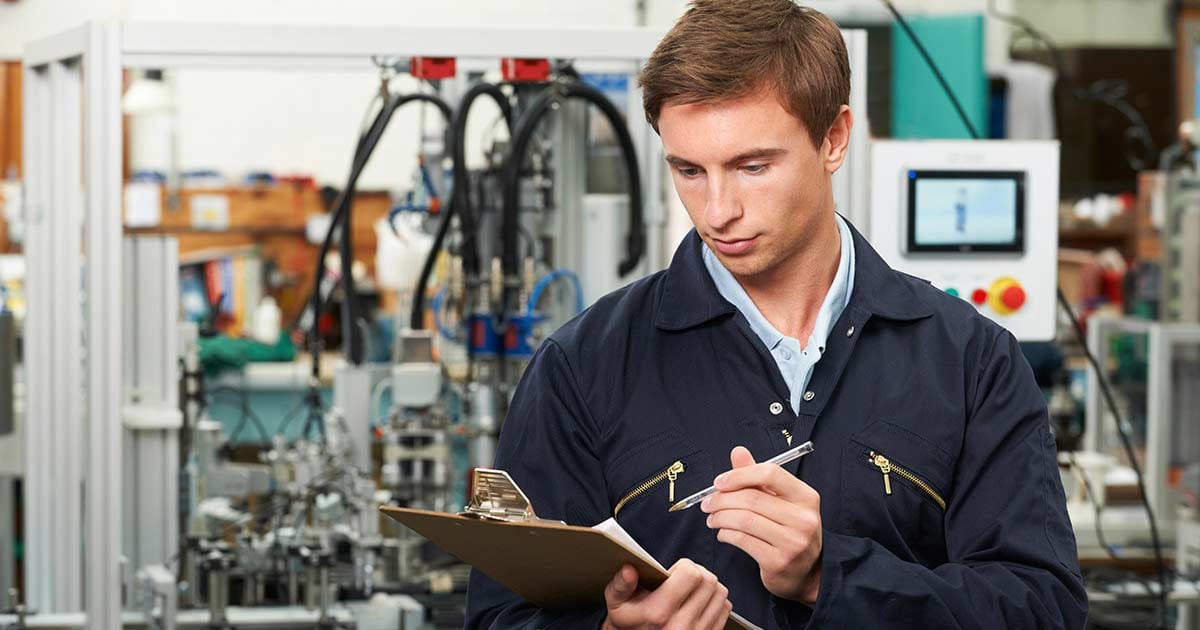
Base your chamber size on these three critical factors:
-
The application test requirements
-
The load size and density
-
The test room conditions
Chambers are used in a wide variety of applications and come in many sizes. Reach in chambers consist of freestanding chambers with casters that typically range from 1 cubic foot to 96 cubic feet in volume, while benchtop chambers can range from .5 cubic feet to 12 cubic feet and are designed to be placed on a working surface or a stand. Walk-in and drive-in rooms can be customized to the required dimensions and will be much larger in size. Floor and benchtop models can be used for small packaging testing to circuit board testing, while walk-ins can accommodate much larger devices under test (DUT). Drive-in chambers can fit up to 6 cars side by side.
Application Test Requirements
If you haven't yet chosen the tests you'll conduct, please check our blog post outlining the necessary test requirements. For many tests, it's recommended to maintain a product volume to total workspace volume ratio of approximately 1:3. This ratio ensures sufficient airflow around the test sample and facilitates comprehensive conditioning across the entire device under test.
It's important to note that the 1:3 ratio may not always be applicable. In the case of highly dense products, a larger workspace might be necessary. Conversely, less dense devices or those designed with ample airflow, like a computer chassis with numerous vents, can occupy a larger proportion of the test volume. Battery testing also has its own specific testing requirements. Refer to our guide on how to buy a battery test chamber.
For environments such as sand, dust, and high-altitude chambers, where the airspeed is already high for product testing, adhering to a strict 1:3 ratio is unnecessary. In these cases, chambers should be slightly larger than the test product to accommodate the specific testing conditions effectively.
Dynamic Load
For products requiring a dynamic load, also called a live load, during testing, a larger chamber may be needed to dissipate heat produced by the DUT, adversely affecting the chamber's pull-down times and humidity system. During testing, products with an active live load produce energy that equates to a considerable amount of heat. Therefore, they require more powerful refrigeration systems to cool down to your specifications. Similarly, heavier and denser products with dead loads may also require more extensive heating and refrigeration systems to achieve desired ramp and pull-down rates. It will take longer to condition the DUT all the way through.
Understanding dynamic load is crucial for selecting an appropriate test chamber for your testing application. If you are conducting battery testing, it is extremely important to understand as it can have a direct effect on your cell testing. Your chosen manufacturer can help you determine the correct test chamber to balance act of the dynamic load and other factors that can alter your testing.
Test Room Conditions
Your test room conditions factor in the choice of chambers. Here are three things to consider.
-
Ambient Room Conditions
External to the test chamber, the ambient condition of the room where the test chamber will be used affects your testing. Test chambers create considerable heat, known as heat rejection, measured in BTUs, and with test cycling up and down the temperature spectrum, the test chambers themselves require good air circulation. Most units need 18-36 inches of clearance in all directions to work efficiently and provide reliable data. Even more critical, test chambers should operate in rooms with an average ambient temperature of 23°C (73.4°F). The constant ambient room temperature will ensure that your test requirements fluctuate when you want them to change. When the ambient temperature in the space where the test chamber is being used continually fluctuates, the test chamber will have to work harder to reach and regulate its programmed setpoints, which will affect the performance and reduce the lifespan of your equipment. The temperature and humidity range of assured performance is between 15°C (59°F) and 25°C (77°F) and 30-50% relative humidity. Work with your facilities manager to understand if the building's cooling and heating units will properly maintain adequate room temperature where the environmental test chamber will operate. -
Footprint
You can generalize an environmental chamber's price into four categories: ovens, benchtops, floor, and walk-in models. Ovens take the least amount of mechanical space because they do not have refrigeration systems and run at a steady temperature. Cycling chambers contain extensive mechanical systems, housing refrigeration (and humidity), in addition to heating systems. Let your available space control your footprint style; if you do not have floor space, can you live with a benchtop model using your desktop space? If you have minimal workspace that you can't give up, consider floor models or stackable benchtops on carts with casters for mobility. Look for where the machine and electrical packs are on a chamber: top, bottom, left, right, or rear. All of these choices will allow you to fit a test chamber into your space with easy access to the test chamber workspace. With these options available, let your laboratory space dictate the style chamber you get. Walk-in test chambers typically have panel walls that, while insulated, are highly susceptible to fluctuations due to surrounding temperature. However, heat rejection can be lowered significantly by placing machine packs outdoors and using water-cooled condensers. -
Mobility
Before deciding which test chamber is right for you, consider where the unit will be located in your building. Will it be a shared unit, and need to move to different areas? Maybe your lab has a hub-and-spoke arrangement with a centralized testing space for all users. Be sure to include discussions with R&D, manufacturing, and operations better to understand the multiple perspectives regarding performance and facility requirements. As previously stated, all our chambers need a max of 18-36 inches of clearance, so you need to account for that in your space, keeping in mind the optimal room conditions for your lab.
CHOOSING TEMPERATURE CHARACTERISTICS
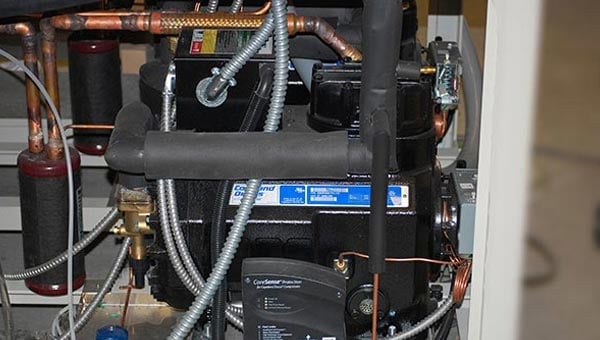
EXPLORING THE DIFFERENT TYPES OF COOLING SYSTEMS
How Cold Do You Need Your Chamber To Be?
Across manufacturers, you will find two types of cooling systems: single-stage and cascade (two-stage) systems. A single-stage compressor refrigeration system typically supports temperatures as low as -37 °C (- 34.6°F) and conforms to many commercial and military standards for low-temperature tests. A cascade refrigeration system should be used to operate with temperatures lower than -40°C. It can generally support temperatures as low as -70°C to -80°C (-94°F to -112°F). The low temperatures obtained with cascade systems occur when two separate, closed refrigerant circuits run concurrently, each using a dedicated refrigerant. As the first stage brings temperatures to a designated low point, the second compressor kicks in to get the first compressor's coolant down to a lower level. This process allows compressors to have a recovery period decreasing stress on the entire system.
The design of the mechanical refrigeration system is critical to the performance you expect. Check that the compressor is self-contained; hermetically and semi-hermetically sealed compressors are virtually maintenance-free. Cooling systems may have a scroll compressor, primarily for smaller test chamber workspaces and small temperature ranges. Because scroll compressors do not have valves, they are significantly more efficient with precise cooling. Discus compressor technology has changed substantially in recent years, making them more efficient. They are still necessary to overcome active live loads and large workspaces. You will find scroll and Discus compressors used in single-stage and cascade cooling systems. It's essential to communicate your low and high-temperature requirements along with the length of time your test will soak at these high and low temperatures. Staying at the extremes on either side for extended amounts of time may change the cooling system configuration.
Choosing between an air-cooled or water-cooled condenser is easier: With water-cooled condensers, the chamber requires a dedicated conditioned waterline. All test chambers can be air- or water-cooled. However, water-cooled units will lower the temperature in the chamber workspace faster than an air-cooled test chamber. Connecting to your existing water-cooled condenser is always an option, or you can consider asking for a self-contained water-cooled condenser onboard your test chamber.
Condenser Comparison |
Air-Cooled |
Water-Cooled |
Heat rejection |
Positive heat rejection |
Little to no heat rejection |
Energy efficiency |
Less efficient |
More efficient |
Footprint |
Larger space requirement |
Smaller space requirement |
Pull-down times |
Slower rate |
Faster rate |
Purchase price |
Less costly for small units |
Less costly for large units |
Installation |
Easy |
Must supply conditioned water cooling loops |
Cooling Systems: Liquid Nitrogen (LN2) and Carbon Dioxide (CO2) Boosts
Liquid nitrogen (LN2) and carbon dioxide (CO2) cooling systems include an attached storage vessel, called a dewar, of either liquid, which is injected into the conditioned airflow area of the chamber, known as the plenum. These liquids evaporate into gas on contact with the inside air of the chamber workspace.
CO2 can lower the chamber's internal temperature rapidly to -70 to -80°C (-94°F to -112°F), while LN2 can quickly lower temperatures to a cryogenic temperature of -185°C (-300°F). LN2 and CO2 boost kits for mechanical refrigeration systems will rapidly decrease the total time to cool down and are often used to rapidly cool your product under test. If you plan to use liquid gas for continuous cooling, you will want a facility line to an outside storage supply, as the test chamber will consume a large amount of coolant. Liquid cooling systems can also act as a backup to mechanical refrigeration systems if they fail.
If either LN2 or CO2 is used, ensure the test chamber is used in a well-ventilated room. Air quality is lowered to dangerous levels as liquid gases dilute the oxygen content, even though both compounds are natural components of the air you breathe. If your facility pipes the gases in, then its ventilation system most likely already vents to the outside directly. Purchasing bottled gas is an option, but consumption could be high, and again, the room must be vented to the outside to ensure the safety of personnel working in the surrounding area.
Environmental Safety
Today, most reputable test chamber manufacturers utilize environmentally friendly hydrofluorocarbon (HFC) refrigerant and chlorofluorocarbon-free (CFC-free) insulation. Check with your manufacturer, though, as using environmentally friendly chemicals is not required, and moving toward these refrigerants aligns with the UNFCCC Paris Agreement to address climate change. Occasionally, compressors will need to be "recharged." If your facility is in a rural area, check that the refrigerants you need are available.
Temperature Change Rate
Temperature cycling is a method used for accelerated life and stress testing, as well as HALT and HASS tests. Therefore, the temperature change rate of an environmental test chamber will be significant when determining which test chamber to purchase.
Variables that affect the pull-down and ramp-up rates include the workspace size, ambient room temperature, clearance around the chamber, temperature range, relative humidity, and power of its heating and refrigeration systems.
Typically, the larger the chamber, and the more extreme the temperature range, the longer the workspace will take to reach the maximum (ramp-up) or minimum (pull-down) temperature.
Usually, more powerful heating and refrigeration systems will be used for larger chambers to keep these larger chambers' change rates consistent with smaller test chambers within the same series.
Another factor that can affect the pull-down rate is whether the refrigeration system is water- or air-cooled. Water-cooled systems of the same size typically lower temperatures faster than air-cooled systems of the same size.
Depending on the temperature range and workspace size, some chambers will take up to two hours to reach the maximum temperature. For example, eight-cubic-foot test chambers can take up to two hours to get to 538°C (1000°F), while workspaces smaller will take about one hour.
Likewise, chambers can take up to an hour to reach their lower limits. With CO2 or LN2 boosts, workspaces will reach -75°C (-103°F) in 15-60 minutes. The time savings add up to around 10 hours based on a 40-cycle testing period.
Chamber manufacturers usually offer options to increase ramp-up and pull-down rates, such as more powerful heating and refrigeration units.
Finally, how air moves around the product and workspace is crucial in environmental testing. As discussed in the "Choosing Chamber Size" section, the general rule of thumb is only to fill one-third of the internal space with products. Always ensure that the product under test is centered in the workspace so air can circulate freely around all sides. Airflow that moves freely through the workspace ensures that the conditioned air can flow evenly through the workspace for accurate and speedy heating and cooling of the products.
If multiple or many smaller products are in the workspace, it's best to spread them evenly throughout the chamber to maximize airflow circulation. When selecting a test chamber, order fully adjustable shelves so you can freely arrange products throughout the workspace with air circulation in mind.
CHOOSING HUMIDITY SYSTEMS
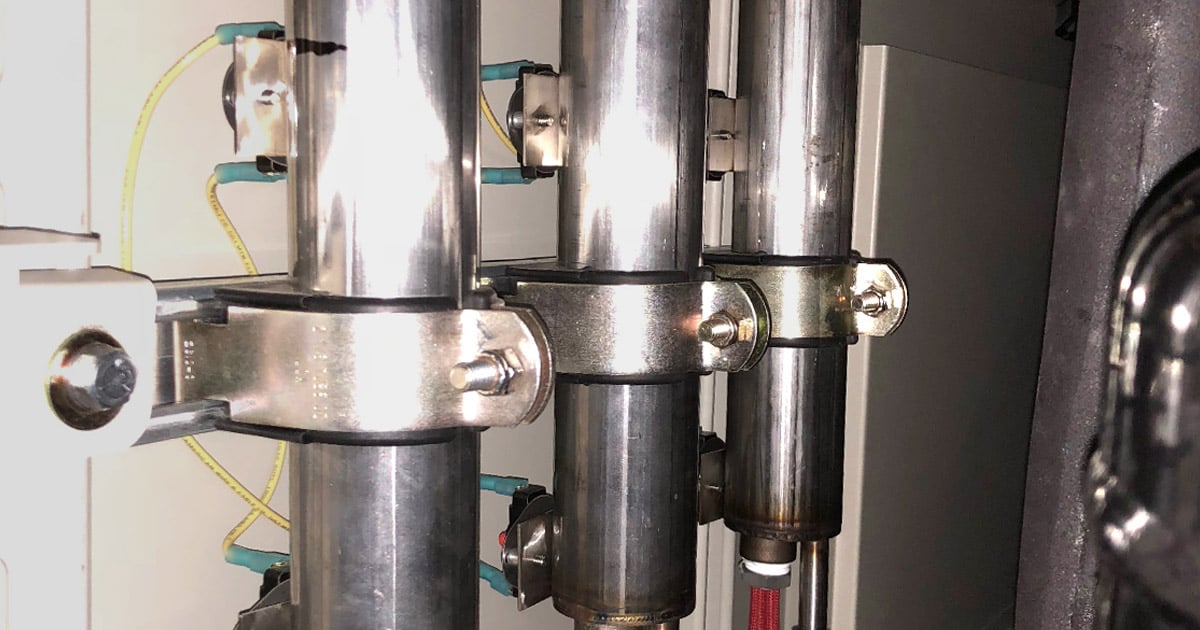
EXPLORING THE DIFFERENT TYPES OF HUMIDITY SYSTEMS
Vapor Generator
The vapor generator is a closed steam generator sized to fit any chamber. Humidity control is optimized and more precise when multiple smaller generators are installed instead of one large steam generator.
When highly-active live loads are being tested, vapor generators may create problems with icing on the refrigeration coils. Increasing the workspace ratio of product-to-working-volume by using a larger chamber is recommended. Share your live load requirements with the manufacturer so you can ensure performance for live load testing.
Atomizing
Mainly used in salt spray chambers, an atomizing nozzle creates fog inside the workspace and requires a direct and constant facility water supply.
Any system using water requires diligent preventative test chamber maintenance.
Humidity Range
The humidity range for most chambers is 10% to 95%, limited by +4°C TD, ±2% Relative Humidity (RH) at the sensor. The RH ranges can extend lower and higher by adding optional features. An external system is needed to achieve dryer conditions, as low as 5% RH.
Obtaining relative humidity above 95% requires an electronic high humidity sensor, which is virtually maintenance-free with calibration accuracy. Dry-bulb/wet-bulb or wet psychrometer systems will increase humidity but require continuous monitoring to maintain proper conditioning of the muslin covers, called wicks. The wick needs regular changing, sometimes even when tests are in process. Using a digital controller, you can monitor, control, and collect data from both extended RH options.
Regular preventative maintenance is required when introducing water to a mechanical system. Across the test chamber industry, you will find that environmental test chambers need conditioned water: water within a specific resistivity or total dissolved solids (TDS) range. You can purchase demineralized or deionized water, but not all bottled water is equal. Not all manufacturers are equivalent when building humidity-enabled test equipment, so know your facility's water quality and compare that to the maker's recommendations to prevent deteriorated systems later on.
Your facility's tap water supply is likely either too clean or too rich in chemicals and mineral content. Therefore, facility water will need conditioning, or you will need to purchase water from an outside source. It's recommended that you send a facility water sample to a qualified independent laboratory to determine the chemical and mineral content in the water supply. City or town water reports only measure at the utility station, not the water in your building. Choose the filtration system to achieve the water quality recommended by your manufacturer.
Demineralizer systems, coupled with filtration, are often options offered by a manufacturer to protect chambers internally. Semi-annual, in-house water testing can measure most chemicals, and a meter can calculate the total dissolved solids in your facility's water. If you use the incorrect water type, it will corrode and eventually destroy the internal workings of a chamber. The damage begins inside the pipes that transport the water, so by the time the naked eye can see a leak, the damage to the water lines is beyond repair, and the lines must be reconstructed.
Percent Relative Humidity (RH%) and Temperature
Electronic Sensor Measurement
Chambers made today are typically equipped with electronic relative humidity sensors as a standard feature. Take time to discuss your product with manufacturers and the need to monitor humidity and temperature levels.
There are many electronic sensors on the market today, and technology is changing fast. Although there's no perfect electronic sensor for all needs, several are available to suit your needs. As humidity moves close to 100%, sensors can have difficulty with accuracy.
The same goes for scenarios where test products release gases when exposed to heat and moisture. When the gases come in contact with typical electronic sensors, the gases stick to the sensor surface, blocking the probe's ability to get an accurate reading. Special sensors can replace standard probes that separate the residues from the gases released in the chamber.
When chambers cycle from high to low temperatures while humidity remains constant, ask for "warmed sensors" to stop condensation from building up on the sensor and giving inaccurate readings. Sometimes, you may resort to old-school methods: Dry-bulb/wet-bulb temperature readings.
Dry-Bulb/Wet-Bulb Measurement (Solid State High Humidity Sensor)
Before electronic sensors were available, engineers and scientists used this method to determine relative humidity and temperature.
Dry-bulb measurement is how most people measure temperature—holding a thermometer tip (aka the bulb) and allowing air to pass by.
Wet-bulb measurement is a process in which you wrap the tip of the bulb in wet muslin, called a wick. This temperature reading will be lower than the dry measurement. The evaporation of the wick and the dry-bulb and wet-bulb readings combined in an equation will determine the humidity in the workspace air. You know humidity is 100% when the dry-bulb and wet-bulb are the same temperatures: achieving complete saturation. Applying the dry-bulb/wet-bulb temperatures on a psychrometric chart will indicate the humidity level. Of course, using a manual calculation and a psychrometric graph is no longer necessary. Today, bulbs have probes to collect temperature readings and the relative humidity displays on your digital controller. A more in-depth controller discussion can be found in the "Controls and Sensors" section.
Few manufacturers and users still choose to use this method because they consistently run environmental tests at high humidity levels. The controller cannot monitor the condition of the muslin wick wrapped around the wet bulb. This manual visual and tactile task is still performed even while test profiles are operating. It's worth mentioning that some users believe dry-bulb/wet-bulb measurements lose accuracy during low-humidity testing conditions. Frequent calibration of the dry and wet bulbs is required. When test chambers are not used for an extended period, the dry- and wet-bulbs will most likely need replacement.
Achieving Low Relative Humidity
Dehumidification systems enable you to operate a chamber at low humidity levels beyond the ability of the refrigeration system evaporators. If you require low-temperature/low-humidity conditioning in your workspace, take time to understand the facility requirements and maintenance needed to operate the dehumidifiers. Each has pros and cons, and the offerings vary across chamber manufacturers.
Desiccant air dryers circulate wet air through a series of drying agents or a drying wheel, recirculating the clean, dry air into the plenum for temperature conditioning.
Another option is a dry-air purge, in which compressed air from an outside supply line is added to the workspace until the RH setpoint is reached. The test chamber's digital controller can manage desiccant air dryers and dry-air purge options.
GN2 and CDA Purges
GN2 (Gaseous Nitrogen) and CDA (compressed dry air) create a dry atmosphere in the chamber. This is to eliminate the possibility of condensation in temperature chambers and control low humidity in humidity chambers.
Controlling and Monitoring Humidity
Most modern test chambers feature programmable, microprocessor-based controllers with:
- Computer communications
- Autotune
- Solid-state RH sensing
- Stainless steel temperature probe inputs
- LED, LCD, or full-color, touchscreen displays showing both process values and setpoint values.
COMPONENTS AND MATERIALS
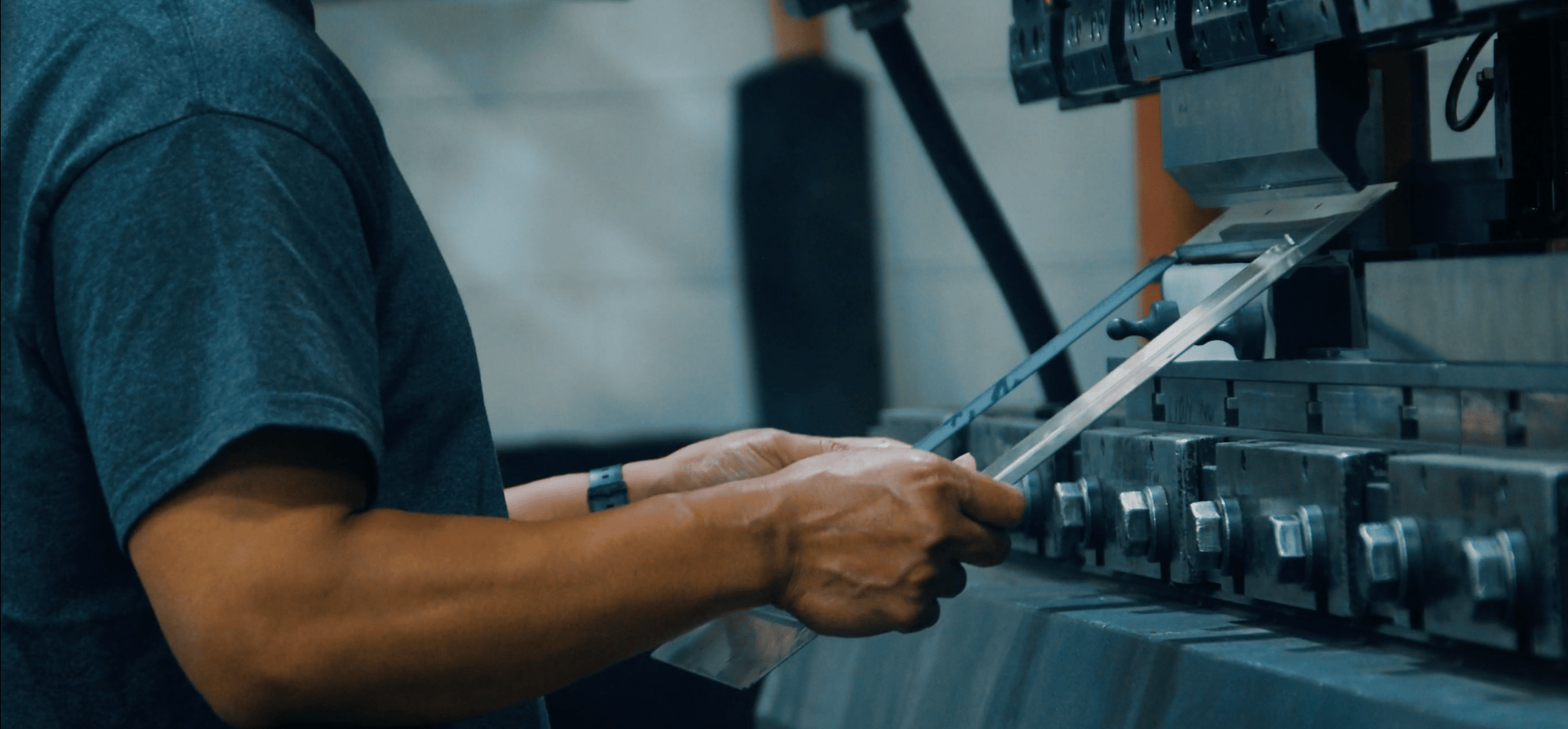
Construction Materials
When purchasing an environmental test chamber, selecting one whose value will remain intact as your company grows and changes is crucial. It's not unusual for a well-maintained test chamber to last for 15 years or more. Ensure the materials used in construction are high-quality and durable to extend your test chamber's life. For smaller test chambers, less than eight cubic feet in volume, confirm the interior workspace walls have at least 304-grade stainless steel with a thickness of at least 18-gauge stainless steel. Larger chambers need a minimum of 18-gauge, sometimes 16-gauge stainless steel with a reinforced floor to ensure adequate durability.
Construction Method
- Internal Workspace: The interior walls of a chamber should be seam-welded. Heli Arc or tungsten inert gas (TIG) welding is preferred to reduce the chance of leaks from inside the workspace to the electrical and mechanical components. Some chambers use riveted wall assembly, which will leak heat and humidity into the insulation and machine compartments.
- Door: The door to the chamber workspace should be fitted with a silicone-type gasket to ensure chamber conditions and prevent leaks. Silicone gaskets can sustain their structure in high and low-temperature conditions. Gasket quality becomes especially essential when CO2 or LN2 is used because other materials quickly disintegrate when exposed to low temperatures.
- Exterior: The outer body of the test chamber should be welded, heavy-gauge, cold-rolled steel. Cold-rolled steel is 20% harder than regular steel, more durable, and has a low tolerance. As a result, it offers a more accurate shape when bent and a better-sealed workspace. These qualities are all critical factors when subjecting machines to high and low temperatures and various humidity levels. Applying powder-coated finishes adds long-term protection against rust, corrosion, and bumps compared to wet-painted finishes.
- Machine Components: Ensure quality craft by applying national standards and organizations' requirements to the wiring, which should conform to the National Electrical Code (NEC). Refrigeration systems should follow the American Society of Heating, Refrigerating, and Air-Conditioning Engineers (ASHRAE) guidelines.
- Insulation: Good insulation will maintain thermal integrity. Placed between the inner and outer walls and inside doors, look for high-density, low "K" factor, non-settling fiberglass or mineral wool insulation. These products are fire retardant and non-corrosive. These materials appear to be in sealed areas, but because of the forced air circulation, check that the insulation materials are thoroughly health- and safety-tested for people that regularly work around test chambers.
DATA COLLECTION
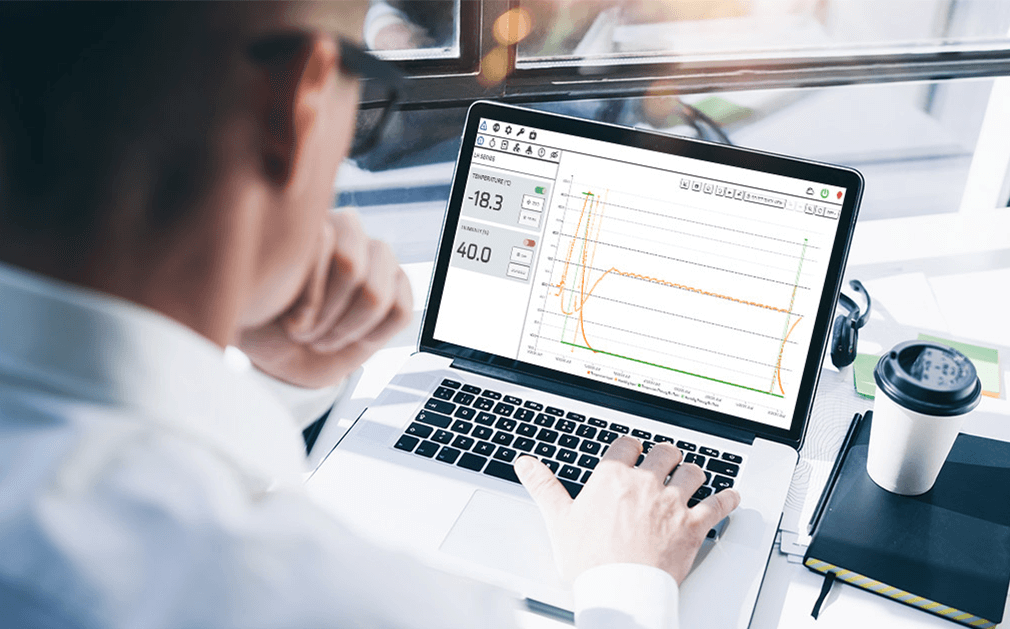
Controller and Data Management Merge:
The technology that controls chambers has simplified programming, operating, and analyzing data anywhere you are. Whether in the lab, at your desk, or at home. Many third-party software products help manage data and make it available to you. AESONE CONNECT, a software and hardware suite, is designed to work hand-in-hand with your environmental test chamber and today's workstyle.
Here's a quick view of what AESONE CONNECT can do for you. Developed by Associated Environmental Systems, it allows you to operate and monitor your test chamber, manage your data, and create test profiles.
AESONE XCHANGE hardware enables any test chamber to expand its accessibility to data by creating a networked system. Never lose your test results with expanded storage that saves up to eight years of data. Even if you have a test chamber made by a different manufacturer, there is a retrofit package for any manufacturer's brand of test chambers.
Decide how you want to use your test chamber:
Operational Control
How will you control the chamber—at the chamber, at your desk, or outside the office? Would you like to be able to turn the test chamber on/off? Do you want to run/pause/stop/start over at any time, even if you're not in the building? Do you need to view the operational setpoints and present values while testing is in progress? How are test profiles built? One person controls all profile building, or is it a shared responsibility? Do multiple test chambers share the same test profile? Do you need to store and move different profiles on and off chamber controllers?
Viewing and Managing Data
Do you need to view your historical data during testing to make real-time decisions? Do multiple team members need access to view operational settings, test progress, and data? Do you need notifications and alarms to signal when test processes begin or end? Would you like to add notes and comments anytime during or after testing at specific datapoints?
Do you need to do all or most of this work remotely? Are team members working separate shifts on the same project? Are they spread out over different locations and need access to operational test monitoring and access to data for analysis?
Security
How will your chamber access your network to share data? How secure is login authorization? Will you need to limit the amount and type of access various team members and users have to chamber operation and data?
Before investing in a test chamber or purchasing third-party software, ask the right questions to meet your needs.
Other Ways to View and Record Data
-
Window
-
Internal Light With External Switch
-
IEEE-488 Computer Interface
-
Circular Chart Recording
-
Electronic Data Recorder
TEST CHAMBER SAFETY FEATURES
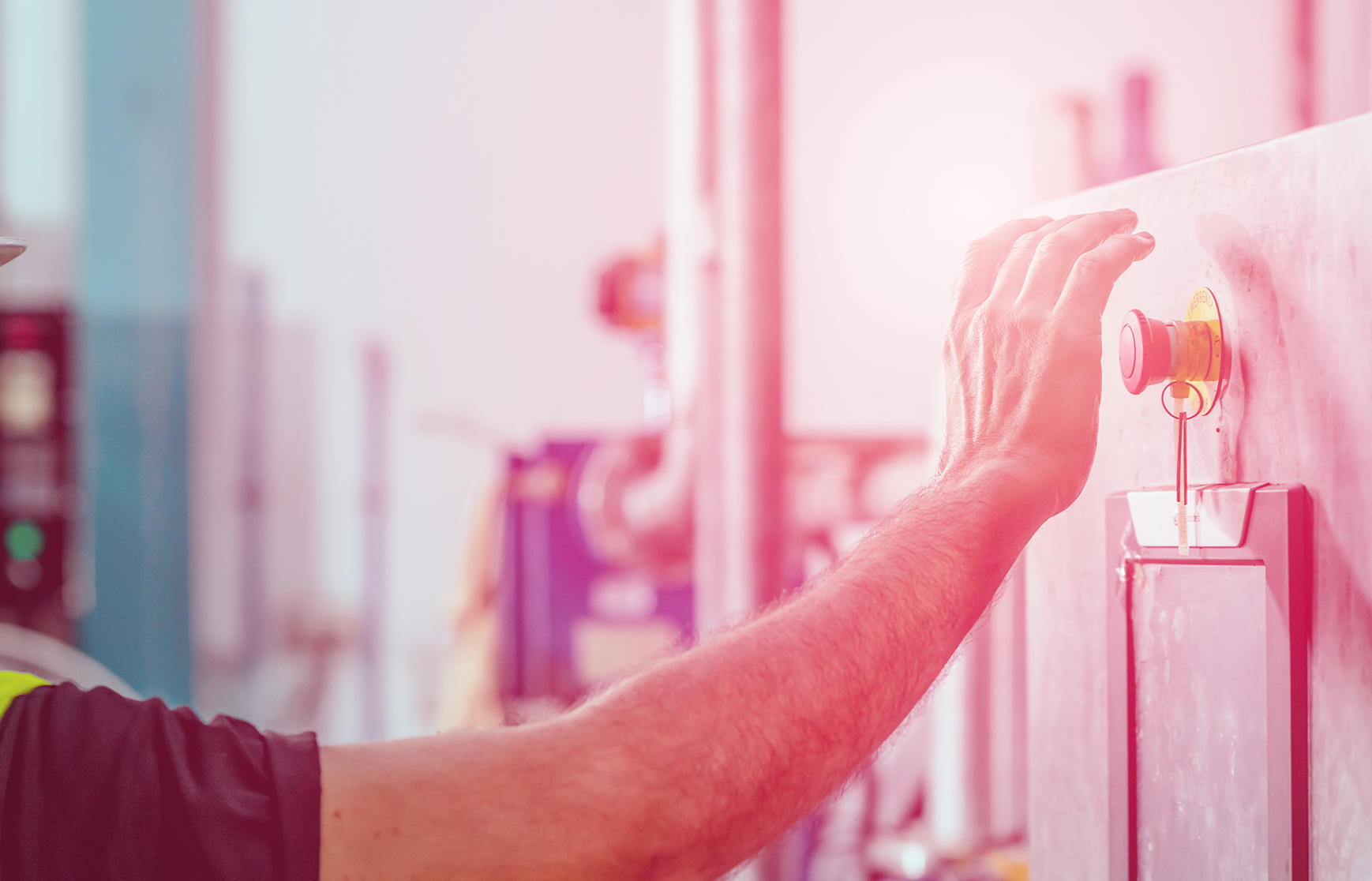
ENVIRONMENTAL TEST CHAMBERS COME STANDARD WITH MULTIPLE FAILSAFES TO PROTECT THE PRODUCT AND YOU.
High-Temperature Failsafe Controls:
Multiple types of temperature failsafes are available. The most common failsafe, which is generally standard with all manufacturers, is the mechanical failsafe. The mechanical failsafe ensures that a product will stay within the setpoint in case the primary controller malfunctions.
Mechanical Failsafe Heat Fuse:
This safety mechanism is used in heating devices to provide failsafe overheating protection. It should be a last resort protection and not a standalone protection. A heat fuse or thermal fuse will interrupt the flow of electricity to the heaters and shut them down if they reach a certain temperature.
Digital High Temp Limit Failsafe:
Most manufacturers will factory set a digital high temp limit failsafe, preventing the heaters from running out of control. As the user, you may dial this down to create your own high-temperature limit: a digital set temperature safety that will shut down the test chamber if it goes over a certain temperature.
Programmable High and Low Temp Safety Indicator:
Once you know your product’s fail points, you can set the chamber to test up to that setpoint and set a safety indicator so the chamber does not exceed the high and low points. This will ensure you’re not causing product failures during production testing.
Noise Reduction Package:
If employees work nearby, you can add a sound-deadening foam to the unit's mechanical portion to lower the chamber's noise output.
Battery Safety Features:
If you purchase a battery test chamber, you will want to look into specific safety features based on your hazard level. Battery testing is inherently dangerous due to its flammable nature and the possible threat of thermal runaway. Chambers can have multiple safety packages in place to prevent and mitigate hazards during testing. These features are very important when purchasing a battery test chamber.
Alternative Power and Other Requirements:
Power. When you look for chambers on manufacturers’ websites, you may find one power option or multiple power options to choose from. Power requirements are determined by your facility’s electrical supply or output. Check with your facilities team to ensure the chamber can be placed in the desired location or a better-suited spot in the building to meet the chamber's power needs. If multiple chambers or other power-draining units are in use simultaneously, the load on the facility might be too high. Check with a qualified electrical engineer to determine your capacity.
Water. If you have ordered humidity or have internal water-cooled refrigeration, you will need a dedicated water supply and a drain. Be diligent when choosing the right test chamber; it needs to fit your test requirements and facility.
ENVIRONMENTAL CHAMBER TESTING SERVICES
.jpg?width=2000&name=test%20chamber%20service%20(1).jpg)
Once you’ve purchased a test chamber, you must make the investment last. The best way to do that is to practice regular maintenance and couple your purchase with a service plan. Work with your manufacturer if possible, as they know your test chamber inside and out.
A service plan ensures you address issues as soon as they arise, spot any defects before they become expensive fixes, and establish a testing schedule with maintenance built into the calendar. The goal is to keep your test chamber operational for as long as possible (upwards of 15 years) while preventing any costly delays.
When considering a service partner, value these qualities:
Availability. Prioritize a service provider that communicates effectively and can access your test chamber promptly. Ongoing testing often runs outside of ‘normal’ work hours, so work with a company that can accommodate your schedule. The other side of availability has to do with parts in stock. If you need to replace a defective piece of your test chamber, you’d like to be able to do so quickly and at a low cost.
Expertise. The best test chamber service companies provide general expertise and demonstrate strong technical skills. They also work on all test chambers, regardless of manufacturer. Consider it: You may have test chambers in your lab that are 10, 15, or even 20 years old from different brands. Calling one service company instead of one for each is ideal.
Customer Service. You rely on your service company to give you honest feedback. What exactly is the problem? How much will it cost to fix? When should I purchase a new chamber rather than continue upkeep on an older one? A company that talks you through your options and sets expectations will stand out from one that’s inflexible.
For more information, we encourage you to read our Guide to Test Chamber Service.
NEXT STEPS
Test chambers come with many features, both standard and optional. Planning ahead of time will make the capital expenditure process easier and free up your valuable time.
To help with that process, we've provided a clickable checklist that outlines all the details to consider for your purchase. Best of luck with your testing.