Before Buying a Test Chamber, Consider Its Temperature Characteristics.
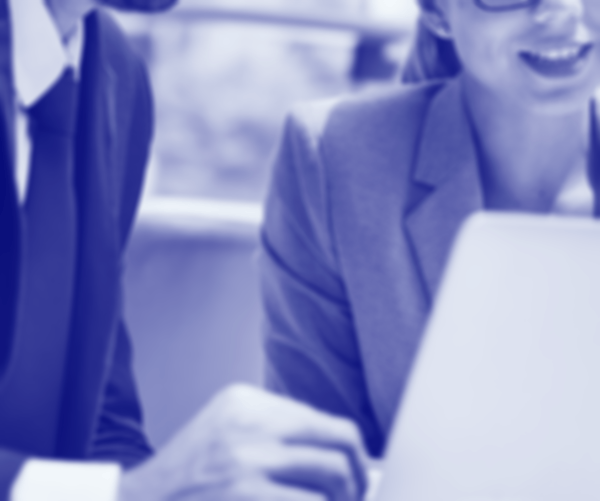
Types of Cooling Systems
How cold do you need to be? Across manufacturers, you will find two types of cooling systems: single-stage and cascade (two stage) systems. The first, single-stage compressor refrigeration system, supports temperatures as low as-37°C (-35°F) and conforms to both commercial and military standards for low-temperature tests. For temperatures below -37°C, a cascade refrigeration system should be used, and can generally support temperatures as low as -73°C (-100°F). The low temperatures obtained with cascade systems occur when two separate, closed refrigerant circuits run concurrently, but each uses dedicated refrigerant and its own compressor.
Low maintenance. The way that mechanical refrigeration systems are designed is critical. Check to see that it is a self-contained system. Choosing a unit that is a hermetically or semi-hermetically sealed unit will make operation and maintenance an easier process.
Air cooled or water cooled? This might be an easy decision: With water cooled condensers, the chamber requires a dedicated conditioned waterline. All chambers can be air or water cooled however water cooled units will lower the temperature in the chamber workspace faster than an air cooled chamber.
Condenser Comparison |
Air Cooled |
Water Cooled |
Heat rejection |
Positive heat rejection |
Little to no heat rejection |
Energy efficiency |
Less efficient |
More efficient |
Footprint |
Larger space requirement |
Smaller space requirement |
Pull-down times |
Slower rate |
Faster rate |
Purchase price |
Less costly for small units |
Less costly for large units |
Installation |
Easy |
Must supply conditioned water cooling loops |
Cooling Systems: LN2 and CO2 Boosts
The Liquid nitrogen and carbon dioxide cooling systems include an attached storage vessel of either liquid, which is injected into the conditioned airflow area of the chamber, known as the plenum. These liquids evaporate into gas on contact with the inside air of the chamber. CO2 can lower the chamber’s internal temperature rapidly to -73°C (-100°F) while LN2 can quickly lower temperatures to a cryogenic temperature of -185°C (-300°F.) LN2 and CO2 boost kits for mechanical refrigeration systems decrease the temperature and total time for a system to cool down and act as a back up to the mechanical refrigeration system if it fails.
If either LN2 or CO2 is used, the chamber must be housed in a well-ventilated room, as the oxygen content of the air is diluted with use of the liquid refrigerant. Both compounds are natural components of air, however constant use can dilute the oxygen content of a room to dangerous levels. If your facility already pipes the gases in, then your facility's ventilation system most likely already vents to the outside directly. Bottled gas can be brought in however, consumption could be high and, again, the room must be vented to the outside to ensure the safety of personnel working in the surrounding area.
Environmental Safety
Today, environmentally-friendly HFC refrigerant and CFC-free insulation are utilized by most reputable test chamber manufacturers. Check with your manufacturer as the use of environmentally-friendly chemicals is not a requirement, but moving toward these refrigerants aligns with the International Paris Climate Agreement.
Temperature Change Rate
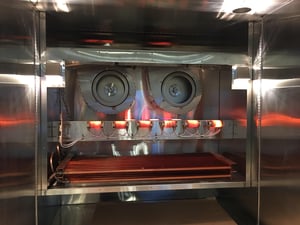
Temperature cycling is a method used in many different HALT and HASS tests; therefore the temperature change rate of an environmental test chamber will be important when determining which chamber to purchase. Variables that affect the pull-down time and ramp up time of a chamber include the chamber size, ambient room temperature, clearance around the chamber, temperature range, and the power of heating and refrigeration systems.
Typically, the larger the chamber, and the more extreme the temperature range, the longer it will take the chamber to reach the maximum (ramp-up) or minimum (pull-down) temperature. Usually, a more powerful heating and refrigeration system will be used for larger chambers to keep these larger chambers’ change rates consistent with smaller chambers within the same series.
Another factor that can affect the pull-down time is whether the refrigeration system is water or air cooled. Water cooled systems typically improve the pull-down time to the minimum temperature opposed to an air cooled system of the same size.
Depending on the temperature range and size, some chambers will take up to two hours to reach the maximum temperature. For example, for a test chamber to reach 538°C (1000°F) an 8 ft3 chamber can take up to two hours, while a smaller chamber will take one hour. Likewise, a chamber can take up to an hour to reach its lower limit. When CO2 or LN2 boosts are added a test chamber will reach -65°C (-85°F) in 15-60 minutes. A time savings of many minutes per cycle, equating to shorter testing periods of sometimes 10 hours (based on 40 cycles).
Usually, chamber manufacturers will have options to improve the chamber ramp-up and pull-down times with more powerful heating and/or a refrigeration unit with more horsepower.
Air Circulation. How air moves around the product and workspace is extremely important in environmental testing. As discussed in the Choosing Chamber Size section, the general rule of thumb is that only ⅓ of the internal space be used for product. This is to ensure that the conditioned air can flow evenly through the workspace. If many smaller products are being tested, it is best to spread the products evenly throughout the chamber to maximize air flow circulation. When selecting a chamber order fully adjustable shelves, so you can freely arrange products throughout the chamber.