Environmental Chambers for Humidity Testing
Industries worldwide need to ensure their products and components are safe before pushing them to market. To fully understand how a product is performing, companies rely on environmental chamber testing to prove the effectiveness (and sometimes ineffectiveness) of the product. In some cases, heat and humidity can lead to failures.
If your product is failing due to heat or humidity, a controlled humidity chamber that can create extreme conditions in a working environment is essential. At Associated Environmental Systems (AES), we manufacture top-of-the-line temperature and humidity chambers that enable users to precisely manipulate settings to meet testing standards. Learn more about humidity chambers and what they can do for you.
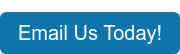
What Is Humidity Testing?
Humidity testing determines how products or devices under test (DUT) withstand real-world conditions by subjecting them to controlled humidity environments. This type of testing is completed using humidity chambers.
What is a Humidity Test Chamber?
These environmental test chambers use vapor generator systems to create specific moisture and heat levels within the chambers’ workspace.
How Does a Humidity Chamber Work?
You may be wondering how a humidity chamber creates these conditions. As the temperature increases, the air’s capacity to hold moisture also increases. That’s what relative humidity (RH) refers to—the level of humidity attainable at a given temperature. Since warmer air holds higher amounts of water, RH at 5 degrees Celsius, for example, will be lower than RH at 20 degrees. This is not to be confused with dew point, which is the temperature at which air must be cooled to condense or form water droplets.
The temperature changes and humidity source must work together to reach the desired setting, informed by industry testing standards. To do this, you need precise control, which test chamber manufacturers like AES can accommodate with an advanced vapor generator system. Vapor generators (closed stainless steel or copper tubes) can be customized to fit any chamber. Multiple generators can also be used for larger workspaces to increase accuracy. Using properly conditioned water, a heating element produces vapor or steam that mixes with conditioned air in a plenum before entering the workspace. You’ll often see manufacturers add demineralizing cartridges to humidity chambers for this purpose.
Electric sensors provide highly accurate readings to ensure the condition of the workspace meets your requirements. This modern system has replaced older methods of creating humidity, such as immersing heaters in water pans or relying on atomizing nozzles (today, you’ll find atomizers on salt spray chambers). Standard humidity chambers feature an RH range of 10% to 95%, with dehumidification coils helping the workspace reach lower humidity levels: The coil attracts moisture, which condenses and drains out of the chamber.
Nitrogen Purge, Dry-Air Purge, and Recirculating Desiccant Purge
High humidity sensors can be added to test chambers to reach an RH as high as 98%. If you need to create conditions less than 10% RH, you can typically do so in three ways:
- Nitrogen Purge: Nitrogen gas is naturally dry, so it is slowly added to the workspace to push out the moisture-laden air. Nitrogen also prevents the oxidation of metals and frost from accumulating on the surface of DUTs.
- Dry-Air Purge Through Desiccant Air Dryer: In a dry-air purge, external compressed air goes through a desiccant system, which absorbs the moisture, before entering the workspace.
- Recirculating Desiccant Air Dryer: Nitrogen or a standard dry-air purge might prove impractical for larger chambers. As an alternative, the chamber air is circulated through a desiccant and then returned to the chamber. Part of the desiccant system, often in the form of a honeycomb wheel, releases captured moisture to the external workspace. The relative humidity you need to reach should be a main point of discussion when purchasing a test chamber.
You can even use a manufacturer-developed dew point calculator to determine if you'll require optional boosts.
Use Cases for Temperature and Humidity Testing Chambers
Across industries, from pharmaceutical to packaging to military defense, temperature and humidity chambers are sought after. Each industry features its own standards (and companies themselves establish internal criteria as well). Here are some common standards that require humidity testing:
- Consumer Electronics, IEC 60601-1: This standard sets the general requirements for medical electrical equipment's basic safety and essential performance, including batteries.
- Military Defense, MIL-STD-810: This standard ensures companies evaluate equipment’s performance when exposed to different environmental conditions and identify any weaknesses.
- Pharmaceuticals, ISO 11135:2014: This standard is required to help companies develop, validate, and routinely control the sterilization process for medical devices.
- Telecommunications: GR-1081: This standard specifies test procedures for fiber optics.
Purchase a Humidity Testing Chamber Today
Once you understand your testing requirements and are ready to move forward with a purchase, get in touch with our team at AES. We will walk you through the purchasing process, guiding you each step of the way.
Tell us your vision, and we’ll work together to build and customize the ideal humidity chamber that meets your needs. View our current environmental test chambers in stock to discover available options. Reach out to a sales engineer to get started!