The AES Guide to Lithium-Ion Battery Test Chambers
BROWSE PRODUCTSKey Considerations for Choosing Lithium-Ion Battery Test Chambers
Few inventions have impacted the modern world as much as rechargeable lithium-ion batteries. In fact, it’s difficult to imagine everyday life without them. They’ve made remote work possible through laptops and mobile devices. They’ve changed the way we enjoy entertainment. They serve a life-saving purpose in streamlining emergency services communication and making portable medical devices, like the automated external defibrillator (AED), possible.
In recent years, they’ve paved the way for the expanse of electric vehicles, with top-of-the-market cars capable of traveling hundreds of miles on a single charge. (Passenger electric planes may not be far behind). Then there’s the crucial role they play in the military and defense.
However, bringing these advanced technologies to market requires hours upon hours of research and design because defective solutions can be potentially dangerous to the public and damaging to brands.
Consider the plight of exploding phones, hoverboards, and more. Companies paid dearly in fines and recalls and endured reputational losses that caused them to lose ground to competitors.
These incidents underscore the importance of safe, accurate testing in R&D and production.
However, battery technology advances only as far as battery testing technology can. So, it’s up to test chambers to facilitate the next great world-changing breakthrough in lithium-ion batteries.
Here’s everything you need to know about battery test chambers.
Battery Basics: Helping Develop the Battery of the Future
Lithium isn’t the only material used in the battery industry. Nickel and lead batteries are standard because of their lower cost. Having said that, lithium-ion batteries' lightweight, high-energy recharging characteristics make them popular for companies across industries.
As evidenced by product failures, there are inherent dangers to working with lithium, the worst being thermal runaway that results in fire and even explosions.
Lithium compounds are popular in batteries for these qualities:
- Lightweight, which makes them ideal for powering portable consumer devices
- Very reactive with a high energy density and fast charges
- Rechargeable, with higher voltages and longer life spans than other battery materials
- Slower discharge compared to other chemicals
There are downsides, however. Lithium compounds are expensive due to a finite supply and dangerous mining. They’re also volatile (the aforementioned thermal runaway risks) and difficult to scale for large applications.
However, as long as consumer demand for portable electronics and electric vehicles remains high, engineers will continue to pour vast resources into developing safe, longer-lasting rechargeable batteries that overcome the material's hazards.
There’s no box that bounds the engineers’ research, from experimenting with chemicals and compounds in search of a replacement for cobalt (a high-cost component of lithium-ion batteries) to exploring new designs in liquid, flow, and solid-state batteries.
Whatever the direction of the battery market, Associated Environmental Systems is working to support research, development, and production by providing efficient ways to test batteries of all styles and sizes.
How Do Lithium-Ion Batteries Work?
Expanding Beyond Lithium Ion Batteries
Lithium isn’t the only material used in the battery industry. Nickel and lead batteries remain standard due to their lower costs. Meanwhile, lithium-ion batteries continue to dominate because of their lightweight, high-energy recharging characteristics, making them popular across industries.
However, as battery research progresses, other chemistries and formats come to life. While lithium-ion batteries remain central to innovation, Associated Environmental Systems (AES) adapts to the industry's growing demands, supporting research and development for a wide range of battery types beyond lithium-ion.
The Importance of a Fully Integrated Battery Tester for Lithium Batteries
When it comes to testing batteries, you have options: You could purchase a battery testing fixture, build one, or outsource your testing.
Let’s start with outsourcing. Some of the biggest companies in the world choose to outsource their battery testing. It could be a matter of convenience—the third-party labs are closer to where they source materials—or preference. For instance, it opens up more time for the company to focus on other aspects of its product, especially if its primary market is not battery-driven.
With outsourced testing, you are on a schedule you cannot control, which can be frustrating if deadlines get pushed. When issues are discovered during testing, design flaws will dramatically increase testing costs. If there is a potential that you have to start from ground zero or restart testing, this will not only increase the cost but also cause testing lead times to be out of your control, possibly delaying your product even more from your anticipated launch date.
Another option is to build your own fixture. If you have experts on your staff who are familiar with the right tools, materials, clips, wires, and energy sources you’ll need, you could probably create a solution to effectively and safely test batteries. But, then you need to see the timing to create the fixture and acquire the chamber. You would need to make sure it fits within the chamber and then can properly test your batteries and safely. Batteries tend to be at risk for thermal runaways, which could take weeks, if not months or years, to create. Would that timeline match up? What if requirements change?
If you want a safe, efficient battery testing fixture, then you need to buy one from a reputable manufacturer. Associated Environmental Systems has developed the ATP series specifically for optimized battery testing.
The Benefits of ATPPRIME:
Patented ATPPRIME gives you a test chamber that is optimized for battery testing. You can modify it for nearly every type of battery: coin, cylindrical, prismatic, pouch, and pack cells. The universal Kelvin connectors enable you to switch between types as well. ATPPRIME is also easy and safe to use, with up to four sliding shelves that accommodate up to 48 channels in total. Manage testing data, including charge and discharge measurements, through the built-in Battery Interface Board (BIB).
Benchtop battery test chambers integrated with ATPPRIME can be stacked to promote efficient small-batch testing.
The Benefits of ATPHEAVY
As demand for electric vehicle batteries with higher power-to-weight ratio increases, so does the need for battery testing technology that can match it. This is precisely where the ATPHEAVY comes in.
ATPHEAVY is also uniquely designed to accommodate large prismatic and pouch batteries for testing up to 1000 AMPS.
ATPHEAVY is compatible with benchtop temperature test chambers, including the Super 508, the most powerful benchtop chamber in the world.
The Benefits of ATPFLEX:
The benefits of ATPFLEX are right in its name. The flexibility allows you to choose a solution that fits your needs. You can select a fixture for a set quantity, cell type, and connector or set up multiple configurations without purchasing a new chamber.
The Benefits of ATPHEAVY ADAPTABLE
ATPHEAVY ADAPTABLE allows for customizable testing. Its modularity allows for creating a custom-tailored application for each test. The board is completely customizable with channel count, current, and format. If requirements change during testing, different holders and adaptors can also be added to the board.
Meet ATPHEAVY ADAPTABLE in our video below!
Test Chamber Safety Features
Phones, laptops, hoverboards, and more don’t just burst into flames for no reason. The culprits often combine environmental conditions and a lack of safety measures for lithium-ion batteries.
These batteries are inherently dangerous, with much energy stored in a small space. Short-circuiting can lead to liquid or gas leaks, fire, or even explosions. That’s why it’s so important to test batteries and the products they power in a controlled, safe environment; you’ll have to prove they won’t fail, and the only way to do that is to identify failure points.
Test chambers have several features that keep lab technicians and engineers safe from unstable batteries. These features are in place to prevent and then mitigate a battery thermal event (BTE).
Keep in mind that testing requirements and standards differ by industry. The nature of your testing will determine the safety features you need, from reinforced doors to gas purges. Here’s a helpful chart:
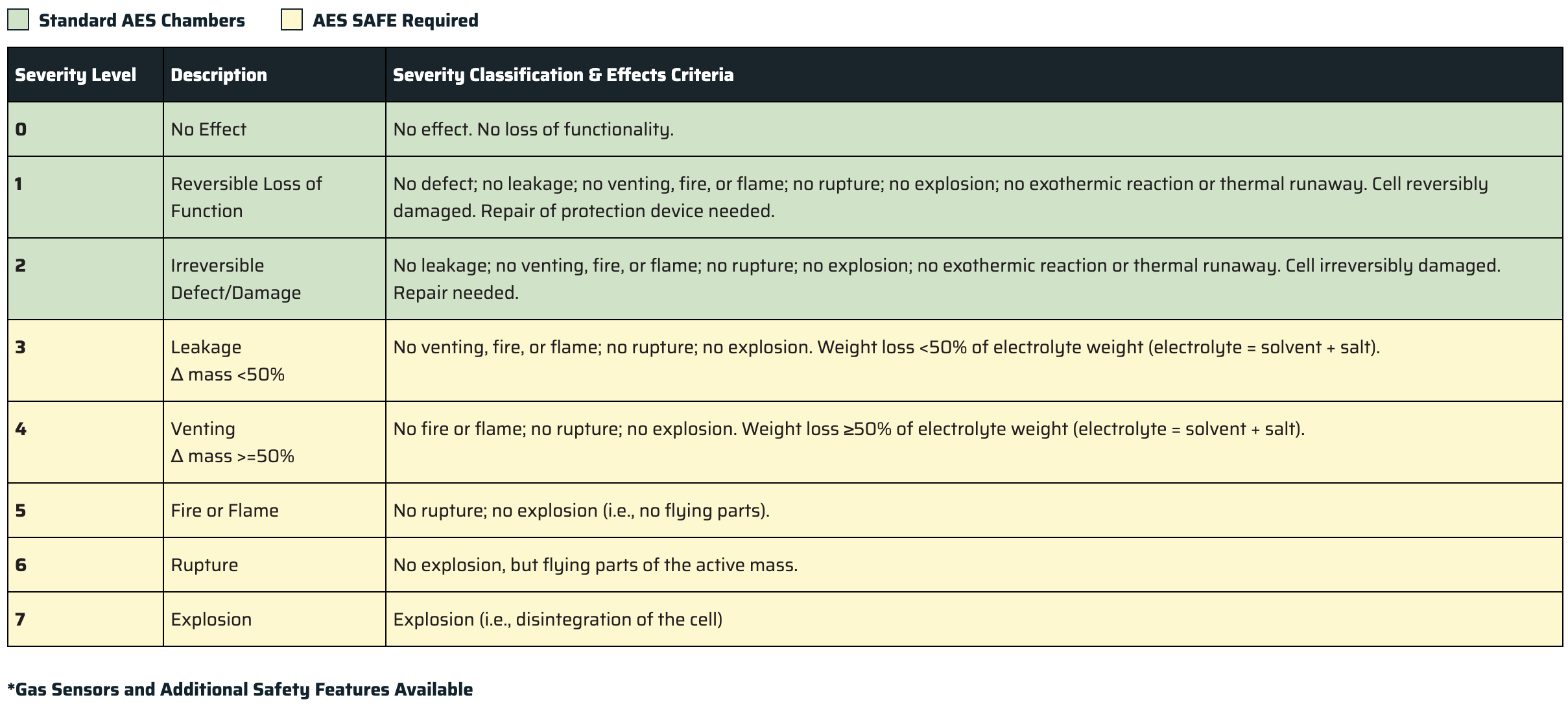
AES Service & Support
A well-maintained test chamber can last 10 years or more, making it essential to pair every purchase with a comprehensive service plan.
Regular maintenance—such as quarterly and yearly checkups—can help catch potential issues early, from a simple door hinge replacement to a necessary recalibration or more complex repairs. This prevents costly downtime and ensures your testing schedule stays on track.
Partnering with a reliable service provider is key. AES’s experienced service team is available for onsite guidance, routine maintenance, repairs, and answering any battery testing questions you may have. They can even help you plan for future upgrades, including replacement chambers.
Best of all, AES services all test chambers models, regardless of manufacturer.
Request More Info
Associated Environmental Systems has customized test chambers for companies in many different industries. We're ready to answer your questions. Please call us at 978-486-5079 or send us a message below.